Cap cooling
LC - LiftCooler
The Lift-Cooler from Eisbär evenly cools your plastic parts using filtered, clean air, directly after ejection - this means greater dimensional stability.
Gallery
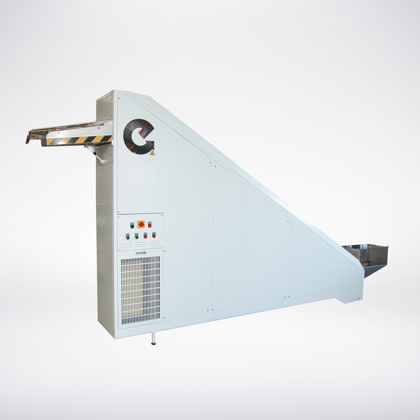
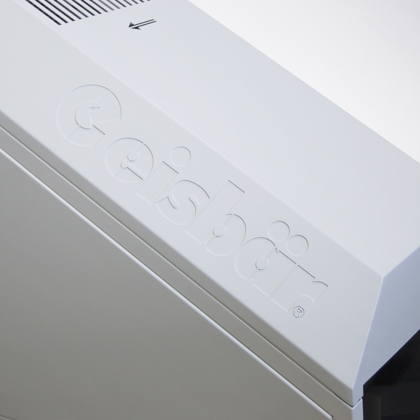
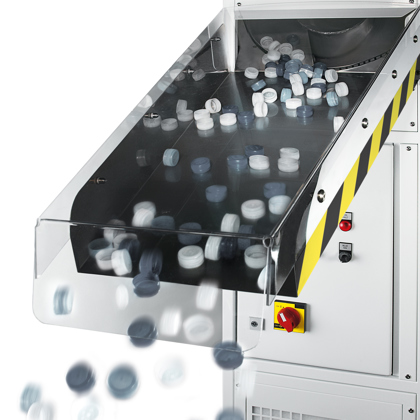
Advantages
- Greater dimensional stability after demolding.
- Low residual heat in the packaging.
- Even temperature of all parts.
- Shorter cycle times.
- Filtered ambient air for cooling → can be used anywhere in the world.
- No cooling water → no microbial contamination due to standing water.
- Food-safe (production parts only come into contact with stainless steel).
- No additional conveying system necessary (transverse conveyor belt extra).
- Easy installation and maintenance.
- Low energy consumption.
Function
The parts enter the LiftCooler via an inlet chute. During the continuous transport, a gentle, clean air flow ensures excess energy is removed and the parts are cooled evenly. At the outlet from the LiftCooler, the parts slide into the intended packaging.
Optionally, a gate ensures a smooth packaging or inspection instrument change.
The low residual heat prevents deformation in the packaging and ensures the highest productivity and product quality.
Technology
- Air flow is continuously adjustable.
- Conveying speed is continuously adjustable.
- Variable cooling time.
- Production parts only come into contact with stainless steel.
LC - TECHNICAL DATA
- Max. throughput: 120,000 caps/h (PCO 1810 2.7 g)
- After tech. clarification max. 200,000 caps/h possible.
- Connected load: 3.4 kW
- Nominal power: min. 0.4 kW; max. 2.9 kW
- Min. filling height (bottom edge of conveyor belt): 415 mm
- Max. discharge height: 1700 mm
- Max. discharge height (with gate): 1565 mm
- Filter class: G3
LC - Service
- Maintenance-free, except regular filter replacement.
- Quick, easy troubleshooting due to system diagnostics and open-access design.
- More than 40 representatives available worldwide.
LC - Installation
- Positioning directly beside the injection-molding machine.
- Quick commissioning.